定量分装机的操作流程可以从以下几个方面进行优化:
一、操作前准备
设备检查与维护
在每次使用定量分装机之前,详细检查设备的各个关键部件,包括电源线、开关、显示屏、输送带、分装头等是否正常。例如,查看电源线是否有破损、插头是否松动;检查输送带是否有磨损、跑偏的情况;观察分装头是否有堵塞或损坏。
定期对设备进行维护保养,根据设备使用说明书制定维护计划。如每周对设备的传动部件添加润滑油,每月对设备的传感器进行校准,每季度对设备的内部进行深度清洁等,以确保设备长期稳定运行。
物料准备与检查
提前准备好需要分装的物料,并对物料进行检查。确保物料的质量符合要求,无杂质、无结块等问题。对于粉末状物料,可以使用筛子进行筛选;对于颗粒状物料,检查是否有较大的杂质或破损的颗粒。
将物料放置在合适的容器中,并确保容器干净、无油污和杂物。容器的大小和形状要根据分装机的要求和物料的性质进行选择,以便于物料的倒入和分装。
参数预设与调试
根据分装物料的特性和包装要求,预先设定好分装机的参数,如分装量、分装速度、分装袋尺寸等。例如,对于精确度要求较高的物料,可以将分装速度设置得较慢,以保证分装的准确性;对于包装袋尺寸有特殊要求的,要提前调整好设备的制袋机构。
在进行实际分装操作之前,先进行几次试运行,观察设备的运行状态和分装效果。如果发现有问题,及时调整参数或设备的设置,直到达到满意的效果为止。
物料填充与输送优化
在物料填充过程中,采用自动化的上料系统,如真空上料机或螺旋上料机,提高物料填充的效率和准确性。避免人工上料带来的误差和物料浪费。
对于输送带的运行速度进行合理控制,根据物料的特点和分装量进行调整。例如,对于易碎的物料,可以适当降低输送带的速度,减少物料在输送过程中的破损;对于流动性较好的物料,可以适当提高输送带的速度,提高生产效率。
称重与检测精准化
定期对称重传感器进行校准和维护,确保称重的准确性。可以采用高精度的称重传感器,并在每次使用前进行零点校准。
在物料分装过程中,设置多重检测机制。例如,当物料重量达到设定值的90%时,预警提示;达到设定值时,自动停止加料;超过设定值时,报警提示并剔除不合格产品。同时,可以采用在线检测设备,如金属检测仪、重量选别秤等,对分装后的产品进行进一步检测,确保产品质量。
数据监控与追溯
安装数据监控系统,实时记录分装机的运行参数、生产数量、不良品数量等信息。通过数据分析,可以发现生产过程中的问题和瓶颈,及时进行优化和改进。
建立产品追溯体系,对每一批次的分装产品进行标识和记录。包括物料的批次、生产时间、操作人员等信息,以便在出现问题时能够迅速追溯到相关的生产和操作环节。
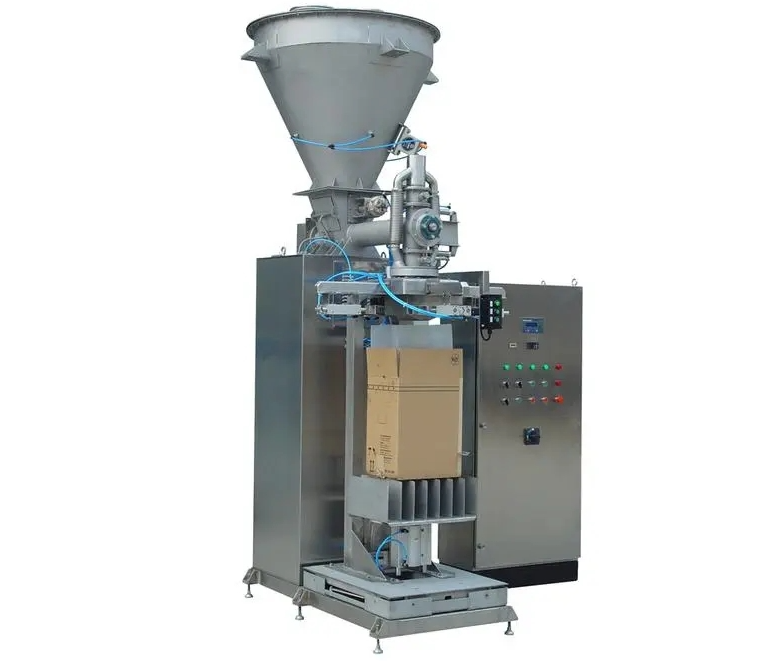